Vous êtes à la recherche d’une méthode simple et efficace pour optimiser la production industrielle de votre entreprise ? Vous voulez réduire les temps de changement de série, augmenter la flexibilité de fabrication et diminuer les coûts de production ? Alors, vous devez connaître le SMED, une technique d’amélioration continue développée par Shigeo Shingo dans les années 1950. Dans cet article, nous allons vous expliquer ce qu’est le SMED, comment il fonctionne, comment l’implémenter et quels sont ses avantages. Suivez le guide !
Introduction à SMED
Historique et contexte de SMED
Le SMED est l’acronyme de Single Minute Exchange of Die, ce qui signifie en français changement d’outil en une minute ou moins. Ce concept a été inventé par Shigeo Shingo, un ingénieur industriel japonais qui a travaillé pour Toyota dans les années 1950 . Shingo a observé que les temps de changement de série étaient très longs dans les usines automobiles, ce qui entraînait des pertes de productivité, des stocks importants et des délais de livraison élevés.
Il a donc cherché à réduire ces temps de changement au minimum, en passant de plusieurs heures à quelques minutes, voire quelques secondes. Il a ainsi créé le SMED, une méthode qui permet de réduire les temps de réglage des machines et d’optimiser la production industrielle.
Définition de SMED
Le SMED est une méthode qui vise à réduire le temps nécessaire pour passer d’une série de fabrication à une autre. Le temps de changement de série est le temps écoulé entre la dernière pièce produite d’une série et la première pièce produite d’une autre série conforme aux spécifications. Le SMED consiste à analyser les opérations de changement de série et à les classer en deux catégories : les opérations internes et les opérations externes.
Les opérations internes sont celles qui doivent être réalisées lorsque la machine est à l’arrêt, tandis que les opérations externes sont celles qui peuvent être réalisées lorsque la machine est en fonctionnement. Le but du SMED est de convertir le maximum d’opérations internes en opérations externes, afin de réduire le temps d’arrêt de la machine au minimum. Le SMED s’inscrit dans la démarche du lean management, qui vise à éliminer les gaspillages et à améliorer la performance des processus industriels.
Comprendre le Processus SMED
Le concept de réglages internes et externes
Pour comprendre le processus SMED, il faut d’abord comprendre le concept de réglages internes et externes. Les réglages sont les opérations nécessaires pour adapter la machine aux caractéristiques du produit à fabriquer. Par exemple, il peut s’agir de changer un outil, un moule, une matrice, une bobine, un paramètre, etc. Les réglages peuvent être classés en deux types : internes ou externes. Les réglages internes sont ceux qui doivent être effectués lorsque la machine est à l’arrêt.
Par exemple, il peut s’agir de démonter un outil usé, de monter un nouvel outil, de régler la pression, la température, la vitesse, etc. Les réglages externes sont ceux qui peuvent être effectués lorsque la machine est en marche. Par exemple, il peut s’agir de préparer le nouvel outil, de vérifier son état, de le transporter près de la machine, de préparer les documents, les consignes, les plans, etc.
La différence entre les réglages internes et externes
La différence entre les réglages internes et externes est essentielle pour le processus SMED. En effet, les réglages internes sont ceux qui provoquent l’arrêt de la machine et donc la perte de production. Les réglages externes sont ceux qui n’ont pas d’impact sur la production, car ils sont réalisés en parallèle du fonctionnement de la machine. Il est donc évident que plus il y a de réglages internes, plus le temps de changement de série est long, et inversement. Le principe du SMED est donc de réduire au maximum les réglages internes et de les transformer en réglages externes, afin de minimiser le temps d’arrêt de la machine et d’optimiser la production.
Transformer des réglages internes en réglages externes
Pour transformer des réglages internes en réglages externes, il faut analyser les opérations de changement de série et identifier celles qui peuvent être réalisées avant ou après l’arrêt de la machine. Par exemple, il peut s’agir de :
- Préparer le nouvel outil à l’avance et le placer à proximité de la machine
- Utiliser des outils standardisés et interchangeables
- Utiliser des systèmes de fixation rapide et sans réglage
- Utiliser des dispositifs de centrage et de positionnement automatiques
- Utiliser des capteurs et des indicateurs pour contrôler les paramètres
- Former le personnel aux bonnes pratiques de changement de série
Ces exemples ne sont pas exhaustifs, il existe d’autres moyens de transformer des réglages internes en réglages externes selon le type de machine, de produit et de processus. L’important est de chercher à simplifier, à standardiser et à rationaliser les opérations de changement de série.
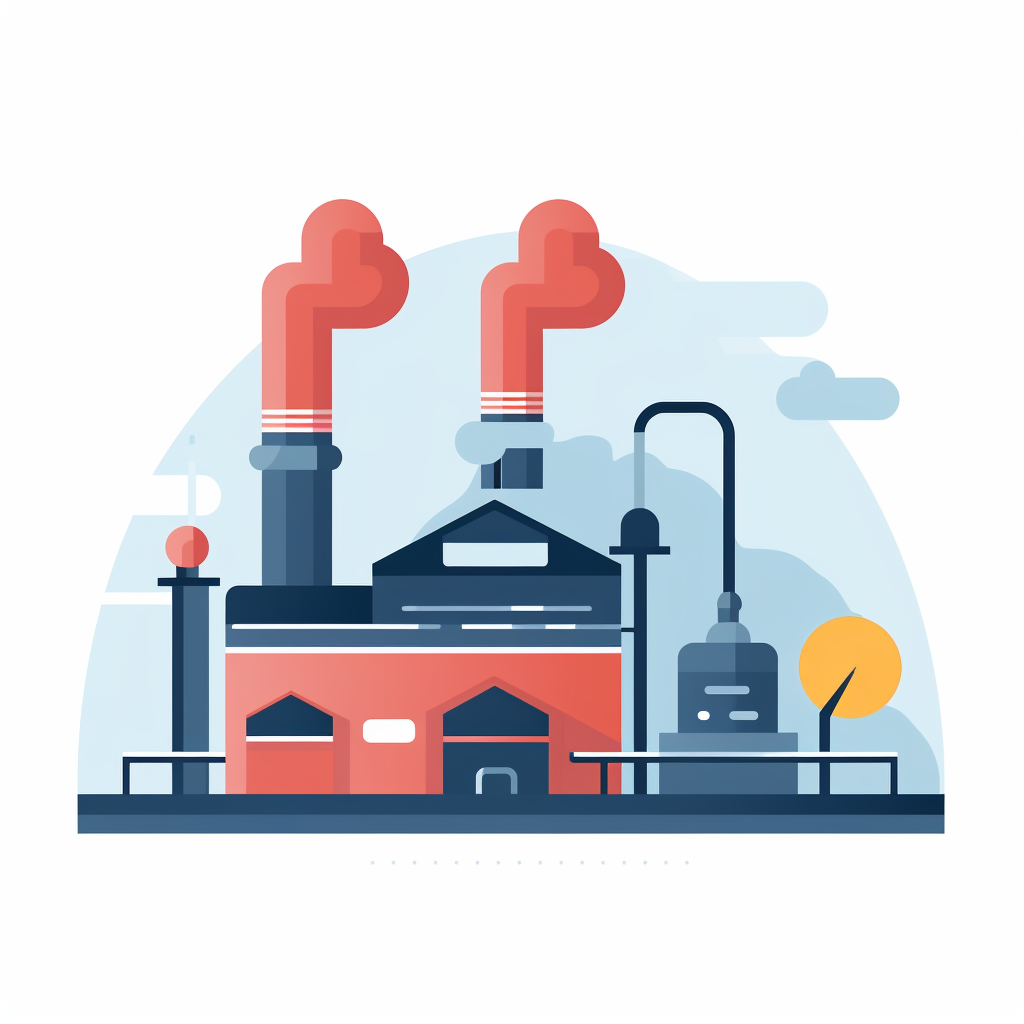
Les étapes de l’implémentation SMED
L’identification des problèmes de production
La première étape pour implémenter le SMED est d’identifier les problèmes de production liés aux temps de changement de série. Il s’agit de mesurer les indicateurs clés tels que le taux d’utilisation des machines, le taux de rendement synthétique, le temps moyen entre les pannes, le temps moyen de réparation, le niveau des stocks, le délai de livraison, etc. Il s’agit aussi d’identifier les machines ou les postes de travail qui ont les temps de changement de série les plus longs et qui ont le plus d’impact sur la production. Il s’agit enfin d’évaluer les causes des temps de changement longs, tels que la complexité des opérations, le manque d’organisation, le manque de formation, le manque d’outils adaptés, etc.
L’observation et l’analyse des processus existants
La deuxième étape pour implémenter le SMED est d’observer et d’analyser les processus existants de changement de série. Il s’agit de filmer ou d’enregistrer les opérations réalisées par l’opérateur lors du changement de série. Il s’agit ensuite de décomposer ces opérations en éléments élémentaires et de les classer en réglages internes ou externes. Il s’agit enfin de mesurer le temps consacré à chaque élément et d’établir un diagramme qui représente le processus actuel. Ce diagramme permettra d’identifier les sources d’amélioration possibles.
Séparation et conversion des processus de réglage
Élimination des déchets et optimisation des processus de réglage
La quatrième étape pour implémenter le SMED est d’éliminer les déchets et d’optimiser les processus de réglage. Il s’agit d’éliminer toutes les opérations inutiles, telles que les déplacements, les attentes, les vérifications, les corrections, etc. Il s’agit aussi d’optimiser les opérations utiles, en utilisant des outils appropriés, en améliorant l’ergonomie, en réduisant les distances, etc. Il s’agit enfin de standardiser les processus de réglage, en établissant des procédures claires, des modes opératoires, des check-lists, etc.
Implémentation et recherche d’améliorations continues
La cinquième et dernière étape pour implémenter le SMED est d’implémenter et de rechercher des améliorations continues. Il s’agit de mettre en œuvre les nouvelles méthodes de changement de série et de former le personnel aux bonnes pratiques. Il s’agit aussi de mesurer les résultats obtenus et de comparer avec la situation initiale. Il s’agit enfin de rechercher des opportunités d’amélioration continue, en sollicitant les suggestions du personnel, en analysant les problèmes rencontrés, en testant de nouvelles solutions, etc.
Les avantages de l’application de la Méthode SMED
Amélioration de l’efficacité de production
L’un des principaux avantages de l’application de la méthode SMED est l’amélioration de l’efficacité de production. En effet, en réduisant les temps de changement de série, on augmente le temps disponible pour la production effective. On peut ainsi produire plus avec les mêmes ressources, ou produire la même quantité avec moins de ressources. On améliore ainsi le taux d’utilisation des machines, le taux de rendement synthétique, le temps moyen entre les pannes, etc.
Diminution du temps de réglage des machines
Un autre avantage de l’application de la méthode SMED est la diminution du temps de réglage des machines. En effet, en passant de plusieurs heures à quelques minutes, voire quelques secondes, pour changer de série, on réduit considérablement le temps perdu à cause des arrêts de production. On peut ainsi répondre plus rapidement aux demandes des clients, réduire les délais de livraison, augmenter la satisfaction des clients, etc.
Réduction des déchets et des coûts de production
Un troisième avantage de l’application de la méthode SMED est la réduction des déchets et des coûts de production. En effet, en réduisant les temps de changement de série, on réduit aussi les quantités de matières premières, de produits semi-finis et de produits finis stockés. On diminue ainsi les coûts de stockage, de transport, de manutention, etc. On réduit également les risques de détérioration, d’obsolescence, de perte, de vol, etc. On diminue enfin les coûts liés aux défauts de qualité, aux rebuts, aux retouches, etc.
Amélioration de la flexibilité de production
Un quatrième avantage de l’application de la méthode SMED est l’amélioration de la flexibilité de production. En effet, en réduisant les temps de changement de série, on augmente la capacité à produire des séries plus courtes, plus variées, plus personnalisées. On peut ainsi mieux s’adapter aux fluctuations du marché, aux besoins spécifiques des clients, aux innovations technologiques, etc. On peut aussi réduire les dépendances vis-à-vis des fournisseurs, des sous-traitants, des partenaires, etc.
Conclusion
L’importance du SMED dans l’industrie moderne
Pour conclure, le SMED est une méthode qui permet d’optimiser la production industrielle en réduisant les temps de changement de série. Le SMED repose sur le concept de réglages internes et externes, et vise à convertir le maximum de réglages internes en réglages externes. Le SMED s’implémente en cinq étapes :
- identification des problèmes de production,
- observation et analyse des processus existants,
- séparation et conversion des processus de réglage,
- élimination des déchets et optimisation des processus de réglage,
- implémentation et recherche d’améliorations continues.
Le SMED présente de nombreux avantages, tels que l’amélioration de l’efficacité de production, la diminution du temps de réglage des machines, la réduction des déchets et des coûts de production, l’amélioration de la flexibilité de production. Le SMED est donc une méthode essentielle pour les entreprises industrielles qui veulent rester compétitives dans un environnement en constante évolution.