Vous avez sûrement entendu parler de la méthode 5S, une démarche d’amélioration continue qui vise à optimiser l’organisation de l’espace de travail, la sécurité, la qualité et la productivité. Mais savez-vous comment faire du 5S dans votre entreprise ? Quels sont les avantages et les étapes de cette méthode ? Comment l’implémenter efficacement et durablement ? Quels sont les exemples d’application du 5S dans différents domaines ? Quelles sont les erreurs courantes à éviter lors de la mise en œuvre du 5S ? Comment poursuivre l’amélioration avec la méthode 5S ?
Dans cet article, nous allons répondre à toutes ces questions et vous donner des conseils pratiques pour réussir votre projet 5S.
Introduction sur la méthode 5S
Définition de la méthode 5S
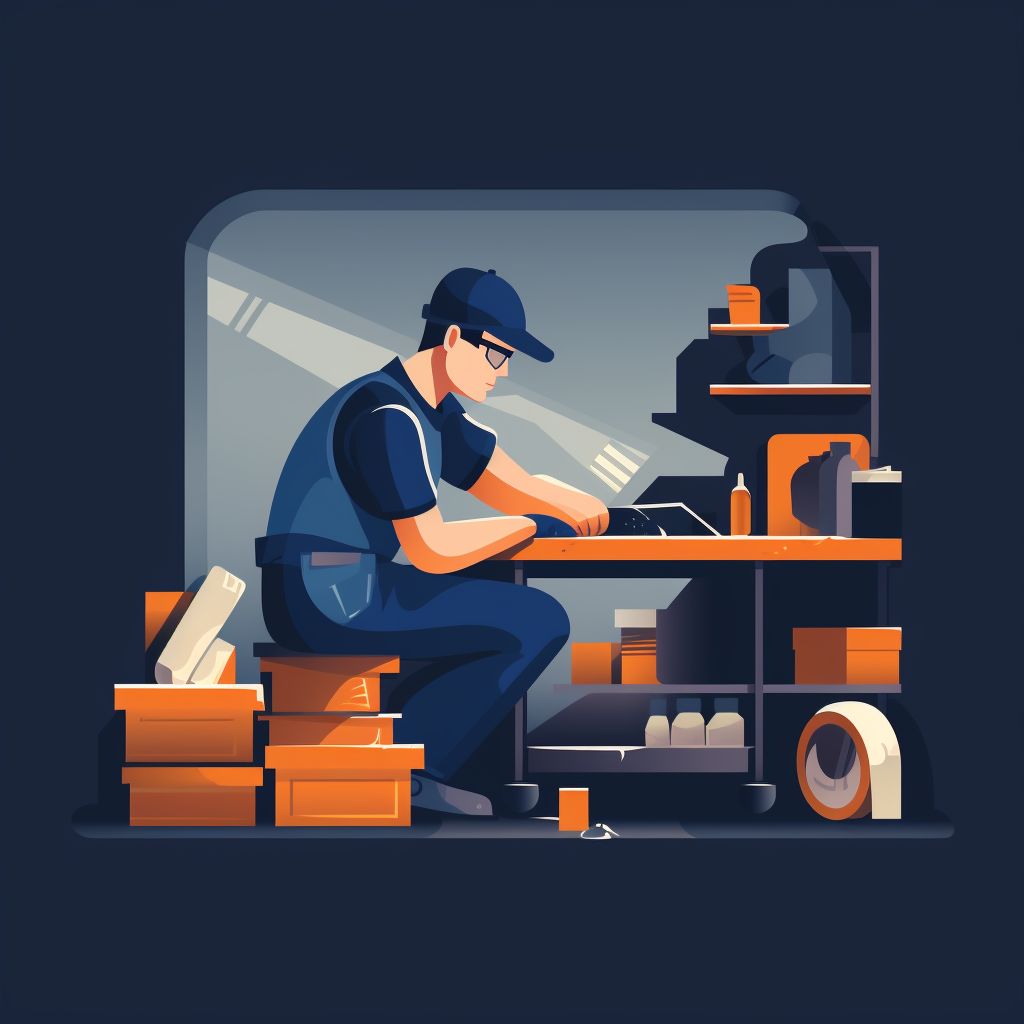
La méthode 5S est une technique d’organisation du lieu de travail qui repose sur cinq principes, dont les noms commencent par la lettre S : Seiri (Supprimer), Seiton (Situer), Seiso (Faire scintiller), Seiketsu (Standardiser) et Shitsuke (Suivre). Ces principes visent à éliminer les éléments inutiles, à ranger les objets utiles, à nettoyer l’environnement, à définir des règles communes et à maintenir les bonnes pratiques. La méthode 5S fait partie du lean management, une approche qui vise à réduire les gaspillages et à maximiser la valeur ajoutée pour le client.
Origines et histoire de la méthode 5S
La méthode 5S trouve ses origines au Japon, dans les années 1950, au sein du système de production Toyota (TPS), qui est considéré comme le précurseur du lean manufacturing. Le TPS est un ensemble de principes et d’outils visant à améliorer la qualité, la productivité et la flexibilité de la production. Le TPS s’inspire notamment des méthodes américaines de gestion des stocks, de contrôle statistique de la qualité et de maintenance préventive. Le TPS intègre également des concepts issus de la culture japonaise, tels que le kaizen (amélioration continue), le jidoka (arrêt automatique en cas d’anomalie) ou le poka-yoke (système anti-erreur).
La méthode 5S est l’un des outils fondamentaux du TPS, qui permet de créer un environnement de travail propice à l’excellence opérationnelle. La méthode 5S s’est ensuite diffusée dans le monde entier, notamment grâce aux travaux de consultants comme Hiroyuki Hirano ou Masaaki Imai. La méthode 5S a été adaptée à différents secteurs d’activité, tels que l’industrie, les services, la santé ou l’informatique.
Comprendre les 5 étapes du 5S
Seiri (Supprimer)
La première étape du 5S consiste à supprimer les objets inutiles ou superflus qui encombrent l’espace de travail. Il s’agit de trier les éléments présents sur le poste de travail selon leur fréquence d’utilisation et leur nécessité. Les éléments inutiles sont éliminés ou déplacés vers un autre endroit. Les éléments utiles sont conservés sur le poste de travail ou stockés à proximité.
L’objectif de cette étape est d’alléger l’espace de travail, de libérer de la place, de réduire les sources de distraction et d’éviter les pertes de temps liées à la recherche d’un objet. Cette étape permet également de réduire les risques d’accidents ou de problèmes liés au stockage excessif, comme la détérioration, l’obsolescence ou le vol.
Seiton (Situer)
La deuxième étape du 5S consiste à situer les objets utiles de manière à ce qu’ils soient facilement accessibles et visibles. Il s’agit de ranger les éléments selon leur fréquence d’utilisation, leur taille, leur forme ou leur fonction. Les éléments les plus utilisés sont placés à portée de main, les éléments moins utilisés sont placés à une certaine distance et les éléments rarement utilisés sont placés dans un endroit dédié.
L’objectif de cette étape est d’optimiser l’espace de travail, de faciliter le flux des opérations, de réduire les déplacements inutiles et d’améliorer l’ergonomie du poste de travail. Cette étape implique également d’identifier les objets par des étiquettes, des codes couleurs ou des symboles, afin de faciliter leur repérage et leur utilisation.
Seiso (Faire scintiller)
La troisième étape du 5S consiste à faire scintiller l’espace de travail en le nettoyant régulièrement. Il s’agit d’éliminer la saleté, la poussière, les taches ou les déchets qui peuvent s’accumuler sur le poste de travail ou sur les moyens de production. Il s’agit également de vérifier le bon fonctionnement des équipements et de détecter les éventuelles anomalies ou dysfonctionnements.
L’objectif de cette étape est d’améliorer l’hygiène et la sécurité du lieu de travail, de prévenir les pannes ou les immobilisations des machines, de prolonger la durée de vie des équipements et d’améliorer la qualité des produits ou des services. Cette étape nécessite la participation active des employés, qui doivent être responsables du nettoyage et de l’entretien de leur poste de travail.
Seiketsu (Standardiser)
La quatrième étape du 5S consiste à standardiser les règles et les procédures relatives aux trois premières étapes. Il s’agit de définir des normes communes pour le tri, le rangement, le nettoyage et la vérification du poste de travail. Il s’agit également d’établir un planning et une répartition des tâches entre les employés. Les normes et le planning doivent être affichés sur le lieu de travail sous forme de tableaux, de check-lists ou de photos.
L’objectif de cette étape est d’harmoniser les pratiques et d’assurer la cohérence entre les différents postes de travail. Cette étape permet également d’évaluer l’état du poste de travail par rapport aux normes établies et d’identifier les écarts ou les points d’amélioration. Cette étape implique la collaboration entre les employés et le management, qui doivent définir ensemble les normes et les suivre.
Shitsuke (Suivre)
La cinquième et dernière étape du 5S consiste à suivre les règles et les procédures établies lors des quatre premières étapes. Il s’agit de maintenir le niveau d’organisation atteint et d’éviter le retour à l’état initial. Il s’agit également d’améliorer continuellement la méthode 5S en tenant compte des retours d’expérience, des suggestions ou des changements dans l’environnement.
L’objectif de cette étape est d’ancrer la méthode 5S dans la culture et les habitudes de travail des employés. Cette étape nécessite la discipline et la rigueur des employés, qui doivent respecter les règles et les procédures. Cette étape requiert également le soutien et l’implication du management, qui doit encourager, reconnaître et récompenser les efforts des employés.
Les avantages de la mise en place du 5S
Amélioration de la productivité
La méthode 5S permet d’améliorer la productivité en réduisant les gaspillages liés au temps, à l’espace ou aux ressources. La méthode permet de mieux connaître la réalité du terrain. En supprimant les éléments inutiles, en situant les éléments utiles en situant les éléments utiles, en faisant scintiller l’espace de travail, en standardisant les règles et en suivant les procédures, la méthode 5S permet de gagner du temps, de réduire les erreurs, d’augmenter la qualité et de satisfaire le client.
Amélioration de la sécurité
La méthode 5S permet d’améliorer la sécurité en prévenant les risques d’accidents ou de blessures liés à un environnement de travail désordonné, sale ou encombré. En supprimant les éléments inutiles, en situant les éléments utiles, en faisant scintiller l’espace de travail, en standardisant les règles et en suivant les procédures, la méthode 5S permet de réduire les obstacles, de dégager les issues de secours, de signaler les dangers et de maintenir les équipements en bon état.
Favoriser le bien-être des employés
La méthode 5S permet de favoriser le bien-être des employés en créant un environnement de travail agréable, propre et confortable. En supprimant les éléments inutiles, en situant les éléments utiles, en faisant scintiller l’espace de travail, en standardisant les règles et en suivant les procédures, la méthode 5S permet d’améliorer l’ambiance, la motivation, la confiance et la fierté des employés. La méthode 5S favorise également la communication, la coopération et le respect entre les employés et le management.
Créer une culture du travail organisée
La méthode 5S permet de créer une culture du travail organisée qui se reflète dans tous les aspects de l’entreprise. En supprimant les éléments inutiles, en situant les éléments utiles, en faisant scintiller l’espace de travail, en standardisant les règles et en suivant les procédures, la méthode 5S permet d’instaurer une discipline, une rigueur et une responsabilité chez les employés. La méthode 5S permet également d’inculquer une culture du lean management, qui vise à améliorer continuellement la performance et la satisfaction du client.
Comment implémenter la méthode 5S ?
Étape 1 : Préparez votre organisation
Avant de mettre en œuvre la méthode 5S, il est important de préparer votre organisation à ce changement. Il s’agit de définir les objectifs, le périmètre, le calendrier et le budget du projet 5S. Il s’agit également de choisir un responsable du projet 5S, qui sera chargé de coordonner les actions et de communiquer avec les parties prenantes. Il s’agit enfin de sensibiliser et d’impliquer tous les employés concernés par le projet 5S, en leur expliquant les bénéfices attendus et en recueillant leurs avis.
Étape 2 : Former l’équipe
Une fois votre organisation prête, il est nécessaire de former l’équipe qui va mettre en œuvre la méthode 5S. Il s’agit de sélectionner un groupe d’employés volontaires et motivés, qui représentent les différents postes de travail concernés par le projet 5S. Il s’agit également de leur fournir une formation théorique et pratique sur la méthode 5S, ses principes, ses étapes et ses outils. Il s’agit enfin de leur donner des consignes claires et précises sur le déroulement du projet 5S et sur leur rôle dans celui-ci.
Étape 3 : Mettre en œuvre les 5S étape par étape
Après avoir formé l’équipe, il est temps de passer à l’action et de mettre en œuvre la méthode 5S étape par étape. Il s’agit de suivre le cycle PDCA (Planifier – Faire – Vérifier – Agir) pour chaque étape du 5S. Il s’agit également d’utiliser des outils visuels comme des photos avant-après, des tableaux de bord ou des indicateurs pour mesurer l’avancement et les résultats du projet 5S. Il s’agit enfin de faire un bilan à la fin de chaque étape du 5S et de célébrer les succès obtenus.
Exemples d’application du 5S dans différents domaines
Exemple d’application du 5S dans une usine de production
Dans une usine de production, la méthode 5S peut être appliquée pour optimiser l’organisation des lignes de production, des ateliers, des magasins ou des entrepôts. Par exemple, en supprimant les éléments inutiles, en situant les éléments utiles, en faisant scintiller l’espace de travail, en standardisant les règles et en suivant les procédures, on peut réduire les temps de changement de série, augmenter le taux de rendement synthétique, diminuer le taux de rebut ou de non-conformité, améliorer la traçabilité des produits ou des matières premières, etc.
Exemple d’application du 5S dans un environnement de bureau
Dans un environnement de bureau, la méthode 5S peut être appliquée pour optimiser l’organisation des postes de travail, des salles de réunion, des archives ou des espaces communs. Par exemple, en supprimant les éléments inutiles, en situant les éléments utiles, en faisant scintiller l’espace de travail, en standardisant les règles et en suivant les procédures, on peut réduire les pertes de documents, augmenter la productivité des employés, diminuer le stress ou la fatigue, améliorer la collaboration ou la créativité, etc.
Exemple d’application du 5S dans un environnement hospitalier
Dans un environnement hospitalier, la méthode 5S peut être appliquée pour optimiser l’organisation des chambres des patients, des salles d’opération, des laboratoires ou des pharmacies. Par exemple, en supprimant les éléments inutiles, en situant les éléments utiles, en faisant scintiller l’espace de travail, en standardisant les règles et en suivant les procédures, on peut réduire les risques d’infection nosocomiale, augmenter la sécurité des patients et du personnel soignant, diminuer les erreurs médicales ou les retards dans les soins, améliorer la satisfaction des patients ou des familles, etc.
Erreurs courantes à éviter lors de la mise en œuvre du 5S
Erreur 1 : Mise en œuvre sans formation suffisante
Une erreur courante à éviter lors de la mise en œuvre du 5S est de se lancer sans avoir formé au préalable l’équipe chargée du projet 5S. Sans formation suffisante sur la méthode 5S, ses principes, ses étapes et ses outils, l’équipe risque de ne pas comprendre l’intérêt du projet 5S, de ne pas respecter la méthodologie du projet 5S ou de ne pas appliquer correctement les règles et les procédures du projet 5S. Il est donc essentiel de prévoir un temps de formation théorique et pratique pour l’équipe avant de démarrer le projet 5S.
Erreur 2 : Manque de participation des employés
Une autre erreur courante à éviter lors de la mise en œuvre du 5S est de négliger la participation des employés concernés par le projet 5S. Sans participation active et volontaire des employés, le projet 5S risque de ne pas être accepté, d’être mal réalisé ou d’être abandonné. Il est donc important d’impliquer les employés dès le début du projet 5S, en leur expliquant les objectifs et les bénéfices du projet 5S, en recueillant leurs avis et leurs suggestions, en leur donnant un rôle et une responsabilité dans le projet 5S et en reconnaissant leurs efforts et leurs résultats.
Erreur 3 : Mise en œuvre trop rapide du 5S
Une troisième erreur courante à éviter lors de la mise en œuvre du 5S est de vouloir aller trop vite dans la réalisation du projet 5S. En voulant mettre en œuvre le 5S trop rapidement, on risque de négliger la qualité du travail, de brusquer les employés, de créer des résistances ou des frustrations, ou de compromettre la pérennité du projet 5S. Il est donc préférable de respecter le rythme et les besoins de chaque étape du 5S, de ne pas sauter d’étapes, de ne pas appliquer le 5S à toute l’entreprise en même temps, mais de procéder par zones ou par services, et de s’assurer que le 5S est bien ancré dans les habitudes avant de passer à la suivante.
Poursuivre l’amélioration avec la méthode 5S
Conserver la discipline et la rigueur
Pour que la méthode 5S soit efficace et durable, il ne suffit pas de la mettre en œuvre une fois, il faut la maintenir dans le temps. Il s’agit de conserver la discipline et la rigueur nécessaires pour respecter les règles et les procédures établies lors des quatre premières étapes du 5S. Il s’agit également de réaliser des audits réguliers pour vérifier l’état du poste de travail par rapport aux normes définies et pour corriger les écarts ou les dérives éventuels.
S’adapter et améliorer continuellement la méthode 5S
La méthode 5S n’est pas une fin en soi, mais un moyen d’améliorer continuellement l’organisation du lieu de travail. Il s’agit donc de s’adapter et d’améliorer constamment la méthode 5S en tenant compte des changements dans l’environnement, des retours d’expérience, des suggestions ou des innovations. Il s’agit également de se fixer des objectifs plus ambitieux et de chercher à atteindre un niveau supérieur de performance et de satisfaction.
Récapitulatif et conclusion
Les principales leçons à retenir sur la méthode 5S
Pour résumer, voici les principales leçons à retenir sur la méthode 5S :
- La méthode 5S est une technique d’organisation du lieu de travail qui repose sur cinq principes : Seiri (Supprimer), Seiton (Situer), Seiso (Faire scintiller), Seiketsu (Standardiser) et Shitsuke (Suivre).
- La méthode 5S trouve ses origines au Japon, dans les années 1950, au sein du système de production Toyota (TPS), qui est considéré comme le précurseur du lean manufacturing.
- La méthode 5S permet d’améliorer la productivité, la sécurité, le bien-être des employés et la culture du travail organisée.
- La méthode 5S peut être appliquée dans différents domaines, tels que l’industrie, les services, la santé ou l’informatique.
- La méthode 5S nécessite une préparation, une formation, une mise en œuvre étape par étape, un suivi et une amélioration continue.
- La méthode 5S requiert la participation et l’implication de tous les employés concernés, ainsi que le soutien et l’encadrement du management.
Conclusion sur la démarche 5S
Pour conclure, nous pouvons dire que la méthode 5S est une démarche d’amélioration continue qui vise à optimiser l’organisation de l’espace de travail, la sécurité, la qualité et la productivité. La méthode 5S est basée sur cinq principes simples mais efficaces, qui permettent d’éliminer les éléments inutiles, de ranger les éléments utiles, de nettoyer l’environnement, de définir des règles communes et de maintenir les bonnes pratiques. La méthode 5S fait partie du lean management, une approche qui vise à réduire les gaspillages et à maximiser la valeur ajoutée pour le client.
La méthode 5S peut être appliquée dans différents secteurs d’activité, tels que l’industrie, les services, la santé ou l’informatique. La méthode 5S nécessite une préparation, une formation, une mise en œuvre étape par étape, un suivi et une amélioration continue. La méthode 5S requiert la participation et l’implication de tous les employés concernés, ainsi que le soutien et l’encadrement du management.
La méthode 5S est donc un outil puissant pour améliorer la performance et la satisfaction de votre entreprise. Si vous souhaitez en savoir plus sur la méthode 5S et vous former en ligne, nous vous invitons à consulter les ressources supplémentaires que nous vous proposons ci-dessous.
Ressources supplémentaires pour approfondir la méthode 5S
Références de livres et de documents sur la méthode 5S
Voici quelques références de livres et de documents qui vous permettront d’approfondir la méthode 5S :
- [5S for Operators: 5 Pillars of the Visual Workplace], par Hiroyuki Hirano, édité par Productivity Press, 1996.
- [Gemba Kaizen: A Commonsense Approach to a Continuous Improvement Strategy], par Masaaki Imai, édité par McGraw-Hill Education, 2012.
- [The 5S Pocket Guide], par James Peterson et Roland Smith, édité par Quality Resources, 1998.
- [The 5S System: Workplace Organization and Standardization], par Productivity Press Development Team, édité par Productivity Press, 2006.
- [Guide pratique du 5S pour les managers et les encadrants], par Xavier Delengaigne et Jean-Marc Legentil, édité par Eyrolles, 2017.
Formation en ligne pour la méthode 5S
Voici quelques formations en ligne qui vous permettront de vous former à la méthode 5S :
- [Lean Management : les fondamentaux], proposé par l’Université Polytechnique Hauts-de-France sur la plateforme FUN-MOOC.
- [Lean Manufacturing : les fondamentaux], proposé par l’Université Polytechnique Hauts-de-France sur la plateforme FUN-MOOC.
- [Lean Six Sigma Yellow Belt : les fondamentaux du Lean Management et du Six Sigma], proposé par l’Université Libre de Bruxelles sur la plateforme edX.
- [Lean Six Sigma Green Belt : maîtriser le Lean Management et le Six Sigma], proposé par l’Université Libre de Bruxelles sur la plateforme edX.
- [Lean Six Sigma Black Belt : devenir expert en Lean Management et en Six Sigma], proposé par l’Université Libre de Bruxelles sur la plateforme edX.
Nous espérons que cet article vous a été utile et que vous avez appris comment faire du 5S. N’hésitez pas à nous faire part de vos commentaires ou de vos questions. Nous vous souhaitons une bonne continuation dans votre démarche d’amélioration continue. 😊