Vous êtes à la recherche d’une méthode efficace pour améliorer la performance de votre usine ? Vous avez entendu parler des AIC en usine, mais vous ne savez pas comment les mettre en place ? Cet article est fait pour vous ! Nous allons vous expliquer ce que sont les AIC, pourquoi elles sont essentielles dans le cadre de l’amélioration continue, comment les organiser et les optimiser, quels sont les équipements et les collaborateurs impliqués, quels sont les exemples concrets et les bénéfices de cette démarche, comment passer à l’ère du digital avec les AIC, et enfin quelles sont les erreurs à éviter et les meilleures pratiques à suivre. Suivez le guide !
Définition et importance de l’AIC dans le milieu industriel
C’est quoi une AIC (Animation à Intervalle Court) ?
Une AIC, ou Animation à Intervalle Court, est un mode de management et d’organisation du travail qui a lieu sur les sites de production. Il s’agit d’une courte réunion (de 5 à 15 minutes) tenue à intervalles réguliers (rotation d’équipe, jour, semaine) au niveau d’un atelier, d’une ligne ou d’un secteur. Les participants restent debout et s’appuient sur le management visuel pour suivre des indicateurs clés et piloter la performance du site. Ces éléments visuels permettent d’identifier en temps réel les écarts de performance afin de réagir rapidement en cas de problème. De plus, l’AIC valorise l’expertise de terrain et la participation active de tous les membres de l’équipe à l’optimisation des processus. Les éventuelles anomalies, ainsi que les pertes de temps, sont visualisées et remontées plus facilement, ce qui encourage tous les acteurs, qu’ils soient opérateurs terrain, superviseurs ou cadres, à proposer des pistes d’amélioration.
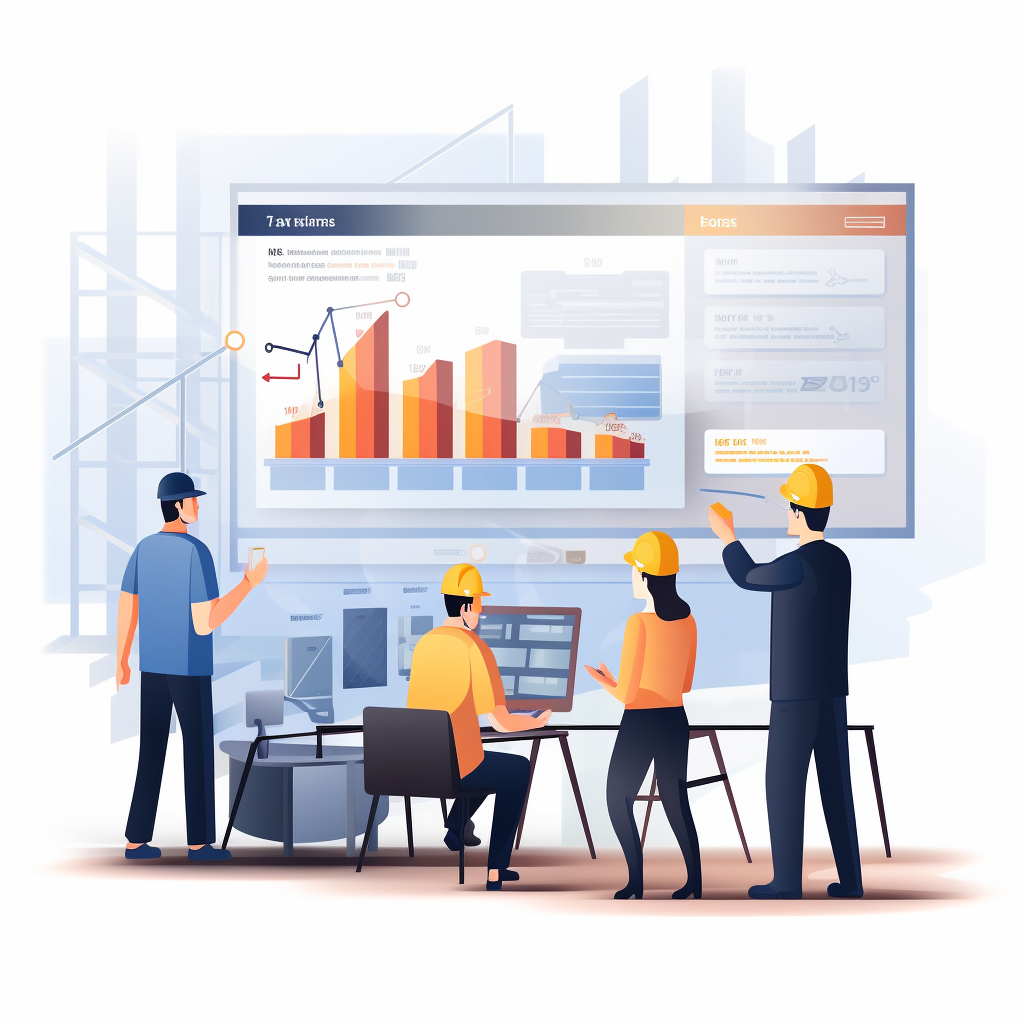
Pourquoi l’AIC en usine est essentielle dans le cadre de l’amélioration continue ?
L’AIC est un outil clé du lean management, une approche globale de gestion des opérations dont l’objectif est d’optimiser les processus de production et à éliminer les gaspillages. C’est pourquoi on appelle aussi ces réunions « AIC lean« . L’AIC permet de mettre en œuvre les principes du PDCA (Plan-Do-Check-Act), un cycle d’amélioration continue basé sur la planification, la réalisation, le contrôle et l’action corrective. L’AIC favorise ainsi la résolution des problèmes à la source, la standardisation des bonnes pratiques, la réduction des coûts et des délais, l’amélioration de la qualité et de la sécurité, la satisfaction des clients et des collaborateurs. L’AIC est donc essentielle pour renforcer la compétitivité et la performance de votre usine.
La mise en place de l’AIC en usine
Le choix stratégique des intervalles
Le choix des intervalles entre les réunions d’AIC dépend du niveau hiérarchique concerné, du type d’activité, du rythme de production et des objectifs visés. Il n’existe pas de règle universelle, mais il faut veiller à ce que les intervalles soient adaptés aux besoins et aux contraintes du terrain. En général, on distingue trois niveaux d’AIC :
- L’AIC opérationnelle : elle concerne les opérateurs terrain et leurs responsables directs. Elle a lieu plusieurs fois par jour ou par rotation d’équipe. Elle vise à suivre les indicateurs opérationnels liés au produit (qualité, quantité, délai) et au processus (temps cycle, taux de rendement synthétique).
- L’AIC tactique : elle concerne les managers intermédiaires et leurs responsables hiérarchiques. Elle a lieu une fois par jour ou par semaine. Elle vise à suivre les indicateurs tactiques liés aux ressources (matières premières, machines, main-d’œuvre) et aux coûts (consommation, productivité, rentabilité).
- L’AIC stratégique : elle concerne les cadres dirigeants et leurs collaborateurs. Elle a lieu une fois par mois ou par trimestre. Elle vise à suivre les indicateurs stratégiques liés aux clients (satisfaction, fidélisation, parts de marché) et aux objectifs (vision, mission, valeurs).
Le choix des intervalles doit être cohérent avec la fréquence des données disponibles, la durée des cycles de production, la capacité de réaction et la marge de manœuvre des acteurs. Il faut éviter les intervalles trop courts, qui peuvent générer du stress et de la lassitude, ou trop longs, qui peuvent entraîner une perte de réactivité et de pertinence.
Organisation des réunions d’AIC en usine
Les réunions d’AIC sont conçues pour être courtes et ciblées. Il est essentiel de fixer une durée précise et de s’y tenir rigoureusement. Cela encourage la discipline et l’efficacité, tout en évitant les dérives et les pertes de temps. Des réunions chronophages peuvent décourager la participation, alourdir l’emploi du temps des présents et nuire à l’impact des actions à mettre en place. Voici les étapes clés pour organiser une réunion d’AIC réussie :
- Définir des objectifs clairs : avant de démarrer une réunion d’AIC, il est essentiel de définir des objectifs clairs. Cela permet à tous les participants de savoir ce que l’on attend d’eux et de se concentrer sur les résultats souhaités. Les objectifs doivent être spécifiques, mesurables, atteignables, pertinents et limités dans le temps (SMART). Cette clarté favorise une compréhension commune et assure l’alignement de l’équipe autour des enjeux clés.
- Préparer les supports visuels : les supports visuels sont indispensables pour animer une réunion d’AIC. Ils permettent de visualiser rapidement les informations pertinentes, de comparer les données réelles aux données prévues, d’identifier les écarts et les causes, de définir les actions correctives et préventives, de suivre leur avancement et leur efficacité. Les supports visuels peuvent prendre la forme de tableaux de bord, de graphiques, d’histogrammes, de courbes, de diagrammes. Ils doivent être simples, lisibles, actualisés et accessibles à tous.
- Animer la réunion : l’animation de la réunion d’AIC doit être dynamique, participative et constructive. Le rôle de l’animateur est de présenter les objectifs, les données, les écarts, les actions, de solliciter les avis, les suggestions, les retours d’expérience des participants, de synthétiser les points clés, de valider les décisions, de conclure la réunion. L’animateur doit veiller à respecter le temps imparti, à impliquer tous les membres de l’équipe, à favoriser le dialogue et la coopération, à reconnaître les efforts et les réussites.
- Assurer le suivi : le suivi est une étape cruciale pour garantir la pérennité et l’amélioration des AIC. Il consiste à vérifier la réalisation des actions décidées lors des réunions précédentes, à mesurer leur impact sur la performance du site, à identifier les points forts et les points faibles du processus d’AIC, à apporter les ajustements nécessaires. Le suivi permet également de communiquer sur les résultats obtenus grâce aux AIC, de valoriser le travail des équipes impliquées, de renforcer leur motivation et leur engagement.
Les outils spécifiques pour optimiser l’AIC
Pour optimiser l’AIC en usine, vous pouvez utiliser des outils spécifiques qui vous aideront à collecter, analyser et partager les données pertinentes pour piloter votre performance. Ces outils peuvent être classés en trois catégories :
- Les outils de collecte : ils permettent de capter les informations utiles sur le terrain, comme le nombre de pièces produites ou défectueuses, le temps passé sur une opération ou une machine, le taux d’utilisation ou d’indisponibilité des équipements, etc. Ces informations peuvent être collectées manuellement, par exemple à l’aide de fiches de relevé, ou automatiquement, par exemple à l’aide de capteurs connectés ou de systèmes d’information intégrés.
- Les outils d’analyse : ils permettent de traiter les informations collectées, de les comparer aux objectifs fixés, de les représenter sous forme graphique, de détecter les écarts et les tendances, d’identifier les causes racines des problèmes, de proposer des solutions adaptées. Ces outils peuvent être des méthodes statistiques, comme le contrôle statistique des processus (SPC), ou des méthodes qualitatives, comme le diagramme d’Ishikawa ou le QQOQCP.
- Les outils de partage : ils permettent de diffuser les informations analysées, de les rendre visibles et accessibles à tous les acteurs concernés, de faciliter la communication et la collaboration entre les équipes, de favoriser l’apprentissage et le partage des bonnes pratiques. Ces outils peuvent être des supports physiques, comme des tableaux blancs ou des panneaux d’affichage, ou des supports numériques, comme des logiciels ou des applications dédiés.
Parmi ces outils, il en existe un qui se distingue par sa simplicité et son efficacité : Shizen. Shizen est une solution digitale qui vous permet de gérer vos AIC en toute facilité. Shizen vous offre les fonctionnalités suivantes :
- La création et la personnalisation de vos tableaux de bord AIC selon vos besoins et vos préférences.
- L’intégration et la synchronisation de vos données provenant de différentes sources (capteurs, ERP, MES, etc.).
- La visualisation en temps réel de vos indicateurs clés et de vos écarts de performance.
- La génération automatique de rapports et de graphiques pour faciliter l’analyse et la prise de décision.
- La planification et le suivi des actions correctives et préventives à mettre en œuvre.
- La notification et l’alerte en cas d’anomalie ou de dérive.
- La collaboration et le partage d’informations entre les différents niveaux hiérarchiques et fonctionnels.
- L’accès sécurisé à vos données depuis n’importe quel appareil (ordinateur, tablette, smartphone).
Avec Shizen, vous pouvez donc faire des AIC en usine très simplement et en gagnant énormément de temps sur la préparation et l’animation des réunions. Vous pouvez également bénéficier d’une meilleure visibilité et d’une meilleure réactivité sur votre performance industrielle. Shizen est utilisé par de nombreux clients satisfaits, comme Schneider Electric, qui a réussi à améliorer sa productivité de 15% grâce à cette solution.
Les équipements et collaborateurs impliqués
Les rôles du personnel dans les AIC en usine
L’AIC est une démarche participative qui implique tous les niveaux hiérarchiques et fonctionnels de l’usine. Chaque acteur a un rôle spécifique à jouer dans le processus d’AIC. Voici les principaux rôles du personnel dans les AIC :
- L’opérateur : il est le premier concerné par l’AIC. Il est responsable de la réalisation des opérations sur son poste de travail. Il collecte les données relatives à son activité. Il participe activement aux réunions d’AIC opérationnelles. Il remonte les problèmes rencontrés sur le terrain. Il propose des solutions pour améliorer son travail. Il met en œuvre les actions correctives et préventives décidées lors des réunions. Il suit l’évolution de ses indicateurs clés.
- Le superviseur : il est le responsable direct des opérateurs. Il organise et anime les réunions d’AIC opérationnelles. Il prépare les supports visuels nécessaires. Il synthétise les informations collectées par les opérateurs. Il facilite la discussion et la résolution des problèmes. Il valide les actions à réaliser. Il assure le suivi des actions et des résultats. Il participe aux réunions d’AIC tactiques.
- Le manager : il est le responsable hiérarchique des superviseurs. Il organise et anime les réunions d’AIC tactiques. Il prépare les supports visuels nécessaires. Il synthétise les informations provenant des différents secteurs ou ateliers. Il facilite la discussion et la résolution des problèmes. Il valide les actions à réaliser. Il assure le suivi des actions et des résultats. Il participe aux réunions d’AIC stratégiques.
- Le directeur : il est le responsable de l’ensemble du site de production. Il organise et anime les réunions d’AIC stratégiques. Il prépare les supports visuels nécessaires. Il synthétise les informations provenant des différents niveaux hiérarchiques et fonctionnels. Il facilite la discussion et la résolution des problèmes. Il valide les actions à réaliser. Il assure le suivi des actions et des résultats. Il communique sur la performance globale du site.
L’AIC nécessite donc une implication forte et une coordination efficace de tous les acteurs de l’usine. Chacun doit être conscient de son rôle et de sa contribution à l’amélioration continue. L’AIC favorise ainsi la responsabilisation, la motivation et la reconnaissance du personnel.
La mobilisation des ressources matérielles
L’AIC en usine requiert également la mobilisation de ressources matérielles adaptées aux besoins et aux contraintes du terrain. Ces ressources peuvent être classées en deux catégories :
- Les ressources physiques : elles comprennent les équipements, les machines, les outils, les matières premières, les produits finis, etc. Elles sont indispensables pour réaliser les opérations de production. Elles doivent être disponibles, fiables, performantes, sécurisées, conformes aux normes de qualité.
- Les ressources numériques : elles comprennent les logiciels, les applications, les systèmes d’information, les réseaux, etc. Elles sont indispensables pour collecter, analyser, partager et stocker les données relatives à la production. Elles doivent être compatibles, intégrées, synchronisées, sécurisées, conformes aux normes de confidentialité.
L’AIC implique donc une gestion optimale des ressources matérielles. Cela passe par une maintenance préventive et curative des équipements, une gestion des stocks et des approvisionnements, une optimisation des flux et des espaces, une digitalisation des processus et des données.
Exemples concrets et bénéfices de l’AIC
Etude de cas : l’implémentation réussie d’AIC en usine
Pour illustrer concrètement l’intérêt de l’AIC en usine, nous allons vous présenter un exemple réel d’implémentation réussie d’AIC en usine de fabrication de produits cosmétiques. Cette usine avait pour objectif d’améliorer sa productivité, sa qualité et sa sécurité tout en réduisant ses coûts et ses délais. Voici les étapes qu’elle a suivies pour mettre en place l’AIC :
- Elle a commencé par former ses équipes aux principes et aux outils de l’AIC.
- Elle a ensuite défini ses objectifs SMART en fonction de ses enjeux stratégiques.
- Elle a choisi ses indicateurs clés de performance en lien avec ses objectifs.
- Elle a déterminé ses intervalles entre les réunions d’AIC selon ses niveaux hiérarchiques.
- Elle a créé ses tableaux de bord AIC avec l’aide de Shizen.
- Elle a intégré ses données provenant de ses capteurs et de son ERP dans Shizen.
- Elle a organisé ses réunions d’AIC en suivant le protocole décrit précédemment.
- Elle a planifié et suivi ses actions correctives et préventives avec Shizen.
- Elle a assuré le suivi et la communication de ses résultats avec Shizen.
Au bout de six mois, cette usine a obtenu des résultats remarquables grâce à l’AIC:
- Sa productivité a augmenté de 20%.
- Sa qualité a amélioré de 15%.
- Sa sécurité a renforcé de 10%.
- Ses coûts ont diminué de 5%.
- Ses délais ont réduit de 10%.
Cette usine est un exemple parmi d’autres de la réussite de l’AIC en usine. Elle témoigne des bénéfices que cette démarche peut apporter à votre usine si vous la mettez en place correctement.
Les bénéfices quantifiables de l’AIC sur la productivité
L’AIC est un levier puissant pour améliorer la productivité de votre usine. La productivité se mesure par le rapport entre la quantité produite et les ressources utilisées. L’AIC permet d’augmenter la quantité produite tout en réduisant les ressources utilisées. Voici comment l’AIC impacte positivement la productivité :
- L’AIC permet d’optimiser le temps de production. En identifiant et en résolvant rapidement les problèmes qui peuvent ralentir ou arrêter la production, comme les pannes, les défauts, les ruptures, les changements de format, etc., l’AIC réduit les temps d’arrêt, les temps morts, les temps improductifs. Elle augmente ainsi le temps utile, le temps cycle, le taux de disponibilité des machines.
- L’AIC permet d’améliorer la qualité de production. En détectant et en éliminant les causes des non-conformités qui peuvent affecter la qualité du produit, comme les erreurs, les variations, les défauts, etc., l’AIC réduit le taux de rebut, le taux de retouche, le taux de non-qualité. Elle augmente ainsi le taux de conformité, le taux de rendement qualité, le taux de satisfaction client.
- L’AIC permet d’optimiser les ressources de production. En analysant et en maîtrisant les consommations des ressources nécessaires à la production, comme les matières premières, l’énergie, la main-d’œuvre, etc., l’AIC réduit les gaspillages, les pertes, les coûts. Elle augmente ainsi l’efficience, la productivité, la rentabilité.
L’AIC en usine permet donc d’améliorer la performance globale en termes de productivité. Selon une étude menée par l’Institut Lean France, les entreprises qui ont mis en place l’AIC ont constaté une augmentation moyenne de leur productivité de 25%.
L’AIC à l’ère du digital
Pourquoi digitaliser votre gestion des AIC ?
Le digital est un facteur clé de compétitivité et d’innovation dans le secteur industriel. Il offre des opportunités et des solutions pour optimiser vos processus de production et vos modes de management. L’AIC n’échappe pas à cette tendance. En effet, digitaliser votre gestion des AIC présente plusieurs avantages :
- La digitalisation vous permet de collecter et d’intégrer plus facilement et plus rapidement vos données provenant de différentes sources (capteurs, ERP, MES, etc.). Vous disposez ainsi d’une vision plus complète et plus fiable de votre performance industrielle.
- La digitalisation vous permet d’analyser et de visualiser plus efficacement et plus clairement vos données grâce à des outils statistiques et graphiques performants. Vous pouvez ainsi détecter plus précisément les écarts et les causes, et proposer des solutions plus adaptées.
- La digitalisation vous permet de partager et de communiquer plus simplement et plus largement vos données avec tous les acteurs concernés (opérateurs, managers, directeurs). Vous pouvez ainsi favoriser la collaboration et l’apprentissage entre les équipes.
- La digitalisation vous permet de planifier et de suivre plus rigoureusement et plus facilement vos actions correctives et préventives grâce à des outils de gestion de projet et d’alerte efficaces. Vous pouvez ainsi assurer la pérennité et l’amélioration continue de vos AIC.
La digitalisation vous permet donc de gagner en temps, en qualité, en efficacité, en réactivité, en visibilité, en collaboration, en performance. Elle vous permet également de vous adapter aux évolutions du marché et aux attentes des clients.
Comment digitaliser efficacement les AIC
Pour digitaliser efficacement les AIC, vous devez choisir un outil adapté à vos besoins et à vos contraintes. Cet outil doit être simple, intuitif, personnalisable, intégrable, sécurisé, évolutif. Il doit également être compatible avec vos équipements et vos systèmes d’information existants. Parmi les outils disponibles sur le marché, il en existe un qui répond à tous ces critères : Shizen.
Shizen est une solution digitale qui vous permet de gérer vos AIC en toute facilité. Shizen vous offre les fonctionnalités suivantes :
- La création et la personnalisation de vos tableaux de bord AIC selon vos besoins et vos préférences.
- L’intégration et la synchronisation de vos données provenant de différentes sources (capteurs, ERP, MES, etc.).
- La visualisation en temps réel de vos indicateurs clés et de vos écarts de performance.
- La génération automatique de rapports et de graphiques pour faciliter l’analyse et la prise de décision.
- La planification et le suivi des actions correctives et préventives à mettre en œuvre.
- La notification et l’alerte en cas d’anomalie ou de dérive.
- La collaboration et le partage d’informations entre les différents niveaux hiérarchiques et fonctionnels.
- L’accès sécurisé à vos données depuis n’importe quel appareil (ordinateur, tablette, smartphone).
Avec Shizen, vous pouvez donc digitaliser vos AIC en usine très simplement et en gagnant énormément de temps sur la préparation et l’animation des réunions. Vous pouvez également bénéficier d’une meilleure visibilité et d’une meilleure réactivité sur votre performance industrielle. Shizen est utilisé par de nombreux clients satisfaits, comme Schneider Electric, qui a réussi à améliorer sa productivité de 15% grâce à cette solution.
Erreurs à éviter et meilleures pratiques
Les pièges courants dans la mise en place des AIC et comment les éviter
L’AIC est une démarche puissante pour améliorer la performance de votre usine. Mais elle n’est pas sans risque. Si elle n’est pas bien conduite, elle peut entraîner des effets indésirables ou contre-productifs. Voici les pièges courants dans la mise en place des AIC et comment les éviter :
- Le manque de formation : si vos équipes ne sont pas formées aux principes et aux outils de l’AIC, elles ne pourront pas participer efficacement aux réunions ni mettre en œuvre les actions décidées. Il est donc essentiel de former vos équipes avant de démarrer l’AIC. Vous pouvez leur expliquer les objectifs, les bénéfices, les étapes, les rôles, les indicateurs, les supports visuels, etc. Vous pouvez également leur faire des démonstrations ou des simulations pour leur montrer comment se déroule une réunion d’AIC.
- Le manque d’implication : si vos équipes ne sont pas impliquées dans l’AIC, elles ne seront pas motivées ni engagées dans l’amélioration continue. Il est donc essentiel de susciter l’adhésion et la participation de vos équipes dès le début de l’AIC. Vous pouvez leur donner la parole, les écouter, les solliciter, les valoriser, les reconnaître. Vous pouvez également leur montrer les résultats obtenus grâce à l’AIC et leur faire part des retours positifs des clients.
- Le manque de cohérence : si vos objectifs, vos indicateurs, vos intervalles ne sont pas cohérents avec votre stratégie, votre activité, votre organisation, vous risquez de perdre en pertinence et en efficacité. Il est donc essentiel de définir des objectifs SMART alignés sur votre vision, votre mission, vos valeurs. Il est également essentiel de choisir des indicateurs pertinents et adaptés à votre niveau d’AIC. Il est enfin essentiel de déterminer des intervalles appropriés à votre rythme de production et à votre capacité de réaction.
- Le manque de suivi : si vous ne suivez pas régulièrement et rigoureusement les actions décidées lors des réunions d’AIC, vous risquez de perdre en efficacité et en crédibilité. Il est donc essentiel d’assurer le suivi des actions correctives et préventives à mettre en œuvre. Vous devez vérifier leur réalisation, mesurer leur impact, identifier les éventuels obstacles ou difficultés, apporter les ajustements nécessaires. Vous devez également communiquer sur les résultats obtenus grâce aux actions mises en place.
- Le manque d’amélioration : si vous ne cherchez pas à améliorer continuellement votre processus d’AIC, vous risquez de stagner ou de régresser dans votre performance. Il est donc essentiel d’évaluer régulièrement la qualité et l’efficacité de votre démarche d’AIC. Vous devez recueillir le feedback de vos équipes, analyser les points forts et les points faibles de votre processus d’AIC, identifier les axes d’amélioration possibles, mettre en place des actions correctives et préventives.
En évitant ces pièges courants, vous pourrez mettre en place des AIC réussies dans votre usine.
Clés du succès pour une implémentation efficace des AIC
Pour conclure cet article, nous allons vous donner quelques clés du succès pour une implémentation efficace des AIC en usine. Ces clés sont issues de notre expérience et de nos observations sur le terrain. Elles sont complémentaires aux conseils que nous avons déjà donnés tout au long de cet article. Les voici :
- Soyez ambitieux mais réaliste : fixez-vous des objectifs ambitieux mais réalisables. Ne visez pas la perfection mais l’amélioration continue. Ne cherchez pas à tout changer d’un coup mais par étapes successives.
- Soyez simple mais rigoureux : choisissez des indicateurs simples mais significatifs. Utilisez des supports visuels simples mais lisibles. Respectez des règles simples mais strictes.
- Soyez cohérent mais flexible : alignez vos objectifs, vos indicateurs, vos intervalles sur votre stratégie, votre activité, votre organisation. Mais adaptez-les en fonction de l’évolution du contexte, des besoins, des contraintes.
- Soyez participatif mais structuré : impliquez tous les acteurs concernés par l’AIC. Mais définissez clairement les rôles et les responsabilités de chacun. Favorisez le dialogue et la coopération. Mais respectez le temps et l’ordre du jour.
- Soyez réactif mais durable : réagissez rapidement aux problèmes rencontrés sur le terrain. Mais ne vous contentez pas de solutions à court terme. Cherchez les causes profondes et les solutions pérennes.
- Soyez innovant mais pragmatique : utilisez les technologies digitales pour optimiser votre gestion des AIC. Mais ne vous laissez pas submerger par la complexité ou la quantité des données. Gardez le focus sur l’essentiel : la performance de votre usine.
En appliquant ces clés du succès, vous pourrez implémenter efficacement les AIC en usine.
Conclusion
Pour résumer, les AIC sont des réunions courtes et régulières qui permettent de suivre et d’améliorer la performance d’une usine. Elles sont basées sur le management visuel, la participation active des équipes, la résolution rapide des problèmes, l’amélioration continue des processus. Elles apportent de nombreux bénéfices en termes de productivité, de qualité, de sécurité, de coût, de délai, de satisfaction client et collaborateur. Elles nécessitent une formation, une implication, une cohérence, un suivi, une amélioration de tous les acteurs concernés. Elles peuvent être optimisées grâce à des outils digitaux comme Shizen. Elles doivent être conduites en respectant quelques principes et en évitant quelques pièges.
Nous espérons que cet article vous a éclairé sur les AIC en usine, comment faire. Si vous souhaitez en savoir plus ou si vous avez besoin d’aide pour mettre en place les AIC en usine, n’hésitez pas à nous contacter. Nous serons ravis de vous accompagner dans votre démarche d’amélioration continue.